PRE-RELEASE
Ignition
Ignition |
General
This ignition function is the one normally used when driving.The ignition timing is regulated depending on the engine load and speed (air mass per combustion mg/c). The objective of this ignition regulation is to obtain the correct combustion pressure build-up.
The combustion pressure should normally attain its maximum value at around 16-17 degrees ATDC. In order to achieve this, the fuel/air mixture must ignite slightly earlier. Normal ignition timing at 2000 rpm, light load, can be around 35 degrees BTDC so that the igniting flame has time to expand and allow the pressure in the cylinder to reach its maximum at the correct point in time.

The expansion rate of the flame varies with the conditions in the combustion chamber, heat, pressure and turbulence. The ignition timing must therefore vary over the engine's load/speed range.
Principle, increasing engine speed
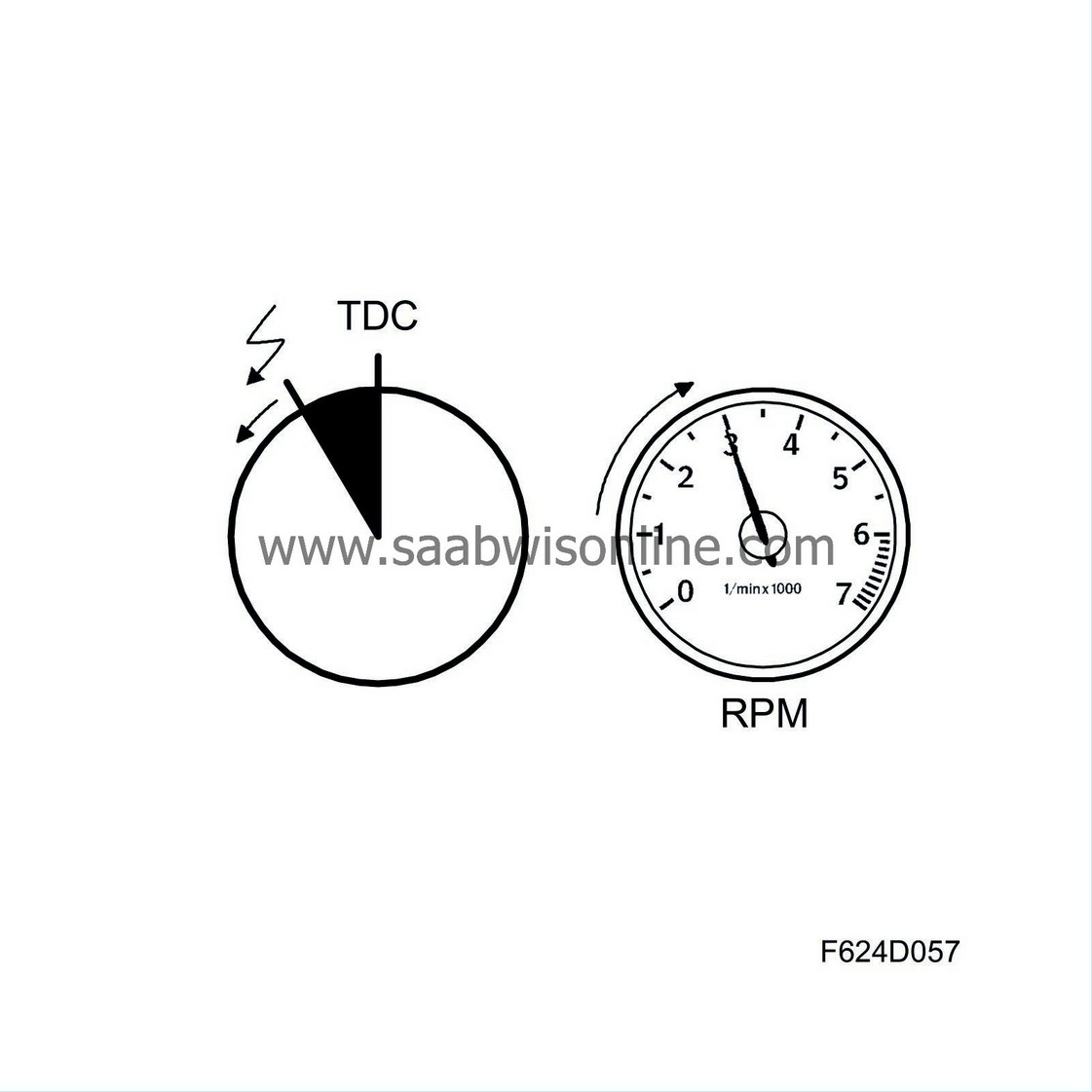
The principle is that the degree of advanced ignition must increase as the engine speed increases or the combustion pressure will build up too late. This would result in poor engine efficiency and exhaust temperature.
Early ignition of the fuel/air mixture would cause pressure to build up too soon, resulting in lower output but increased knock sensitivity.
Principle, increasing load
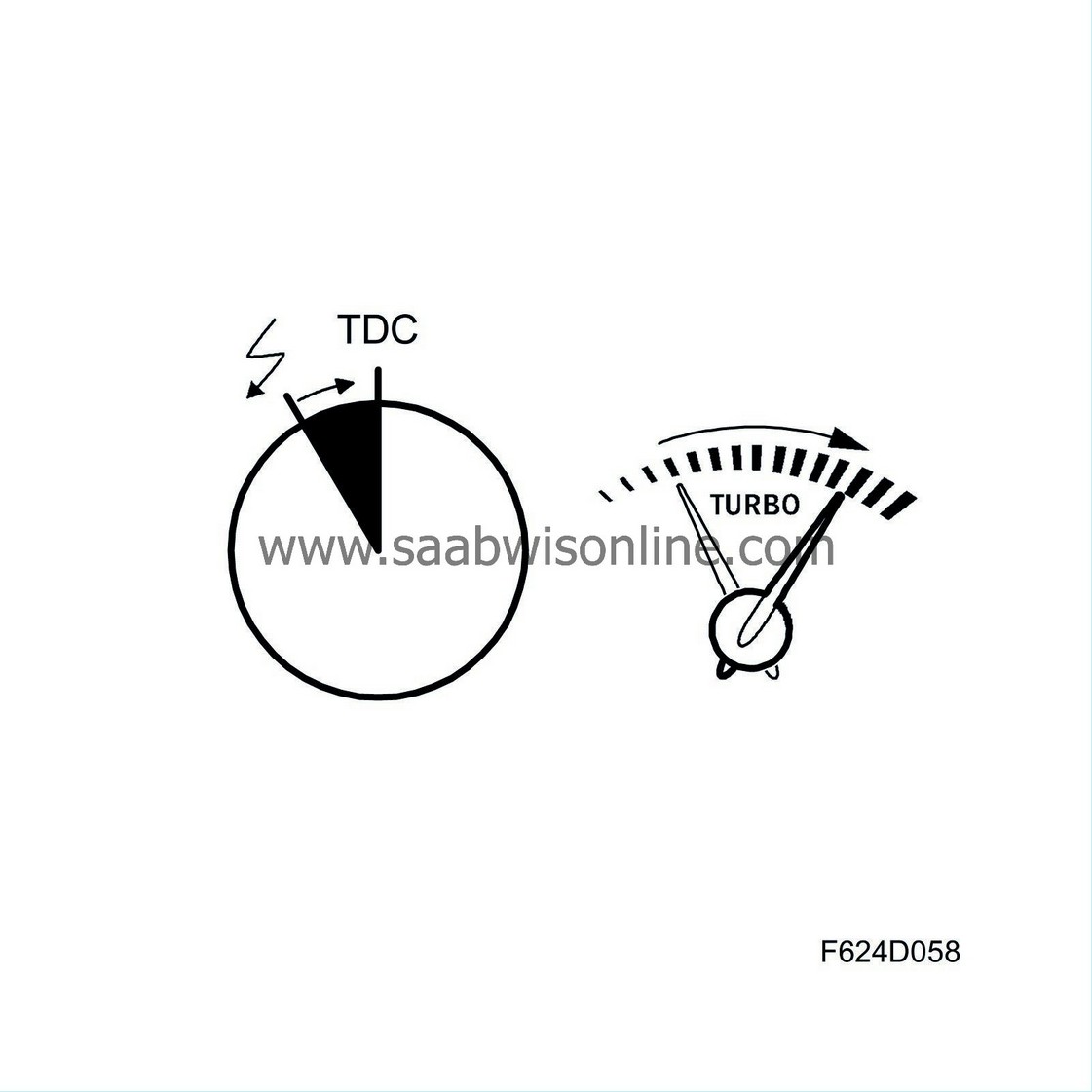
With increasing load (air mass/combustion), the pressure, temperature and turbulence in the cylinders will also increase, as will the combustion rate.
Normal ignition timing at 2000 rpm and wide open throttle can be around 12 degrees BTDC, compared with 35 degrees with a light load at the same speed.
The difference in ignition timing is reflected in the difference in combustion rate between high engine loads and low engine loads. Consequently, the ignition timing must be retarded at high engine loads.
Optimisation
A matrix (map, kennfeldt) in the control module memory contains the ignition timing for each respective load and engine speed.Ignition timing is optimised to find the best compromise between torque in the actual operating point, which is also the best efficiency and thereby best fuel economy, and NOx and CO emissions.
Normal ignition timing that is the basis for ignition timing control when driving must occasionally be compensated to a slightly more advanced or retarded ignition timing due to other factors than just load and engine speed.
Start-up ignition timing |

General
This function is used to calculate the actual ignition timing upon engine start.Starting ignition is active from the time the engine is stopped until engine speed reaches 500 rpm. Ignition timing for starting ignition is regulated based on engine speed and coolant temperature. Normal ignition timing for starting ignition if engine coolant temperature is 20°C is 10 degrees BTDC.
To compensate the differences in the expansion rate of the flame, ignition timing when starting must vary depending on the engine coolant temperature. At low temperatures, the flame will expand slowly in the combustion chamber. In order for the pressure in the cylinder to reach its maximum value at the correct crankshaft position, ignition timing must consequently be relatively advanced when the coolant temperature is low.
Conversely, the flame expands quickly when temperature is high. Ignition timing must then be slightly retarded. Otherwise, the pressure in the cylinder would reach high values BTDC, which would result in the engine starting hard with spiking sounds.
During slow starter motor cranking, ignition timing is retarded slightly. When the engine speed during starter motor cranking is high, ignition timing must be set to a more advanced position. This is to compensate for the flame expansion rate.
Once the engine has started, ignition timing from the start function will be increased to the value from the idling speed ignition timing.
Principle, low coolant temperature
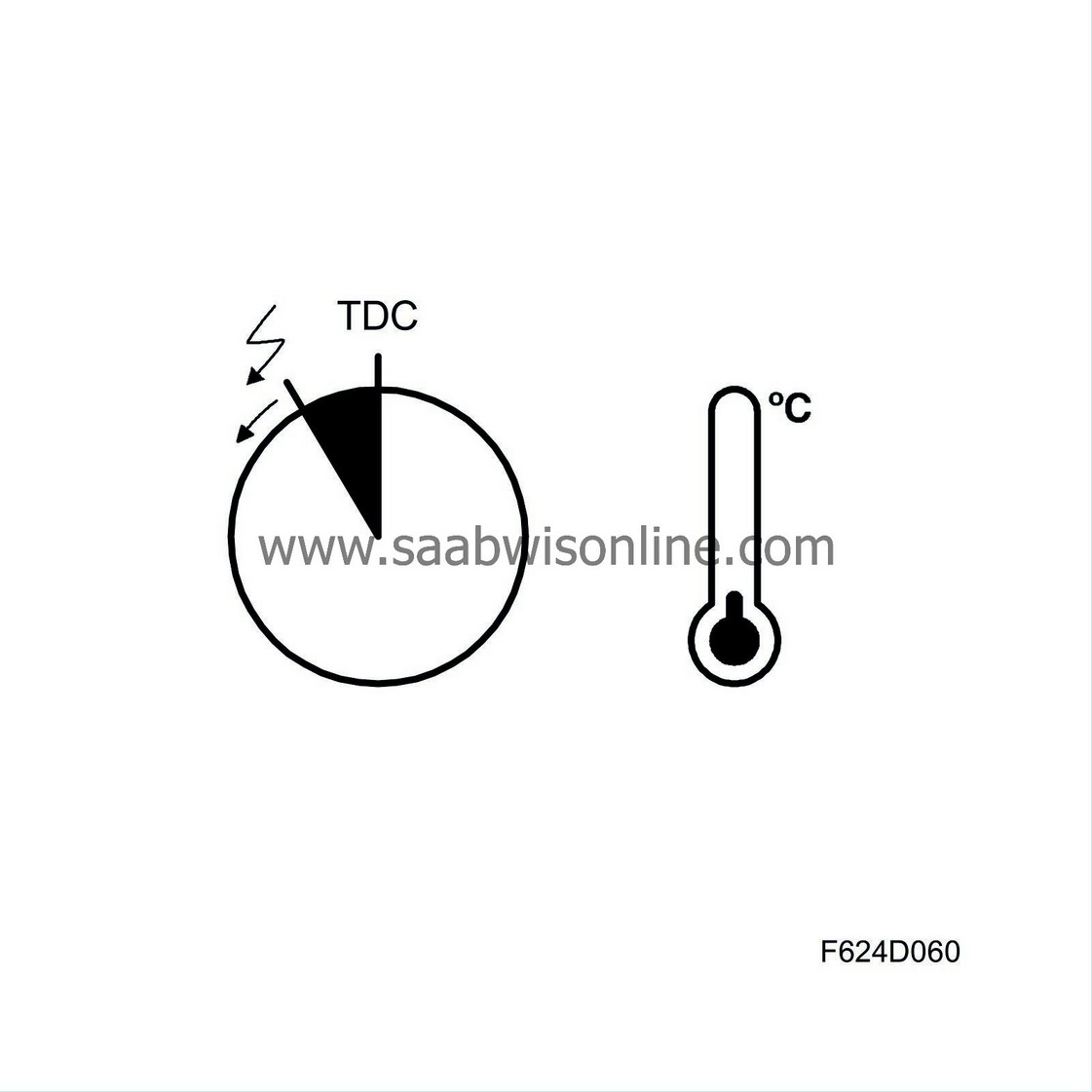
Low coolant temperature results in advanced ignition timing to compensate for the lower combustion rate at low temperatures.
Principle, high coolant temperature
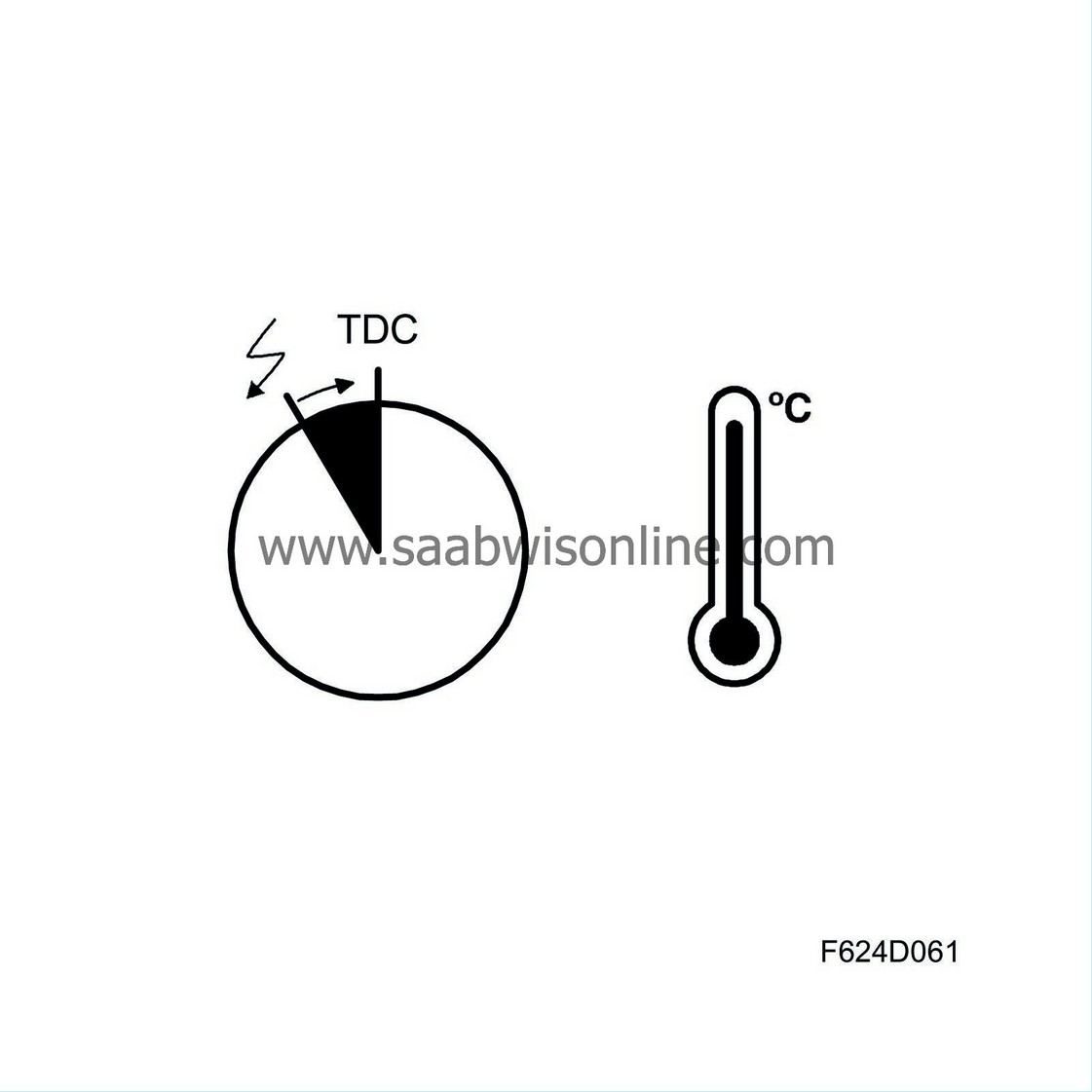
High coolant temperature results in retarded ignition timing to compensate for the higher combustion rate at high temperatures.
Idle speed ignition timing |
General
The ignition timing applicable at idling speed is determined mainly by the engine load/speed. But this can be compensated by the effect of various parameters. The idling speed ignition timing function is active during idling. (Accelerator pedal released).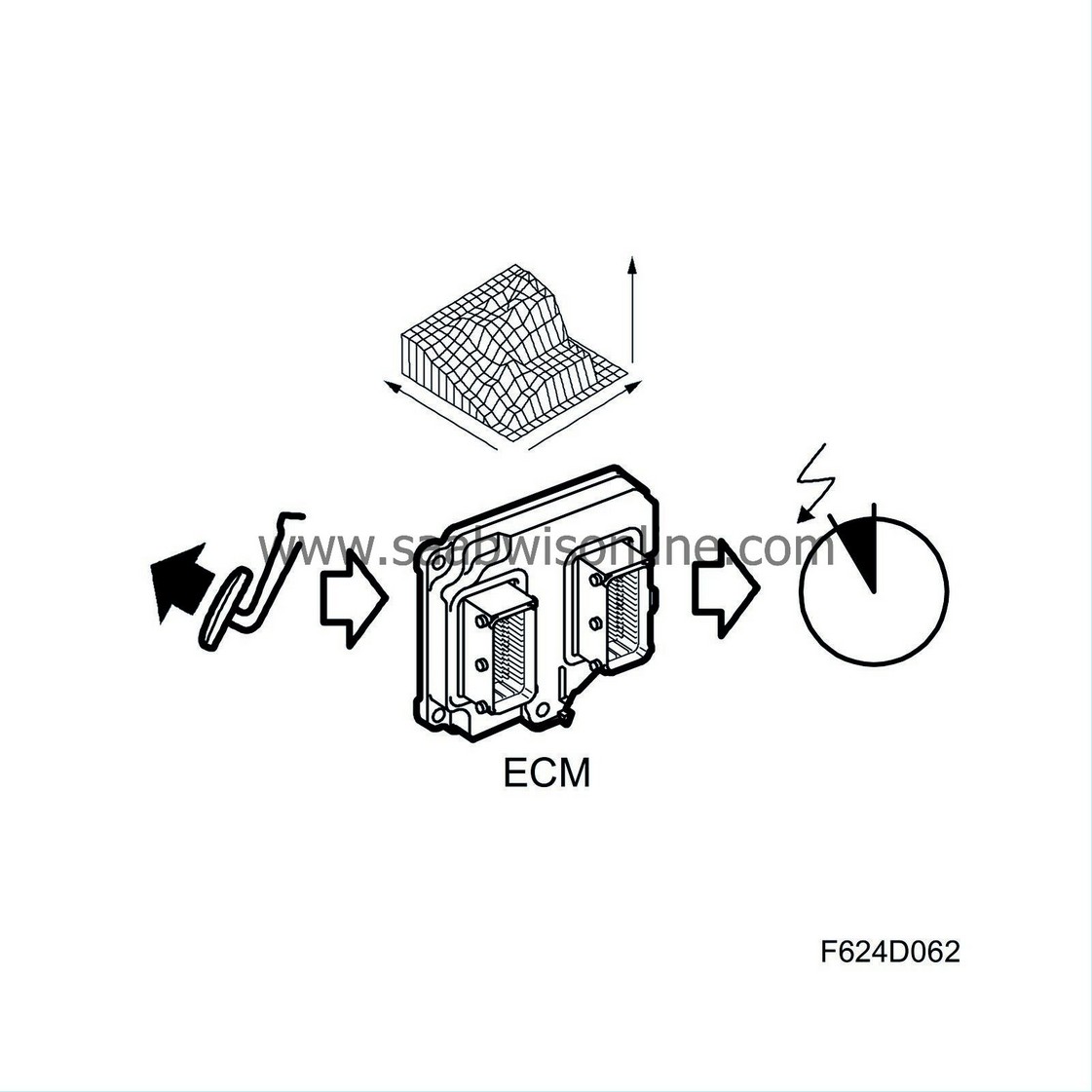
Basic matrix for idling speed ignition timing, principle
The basic value for idling speed ignition timing is based on engine load and speed. This is called "basic value idling speed ignition timing."Ignition timing is slightly later than optimal to obtain a torque reserve, i.e. the possibility of increasing engine torque quickly through advanced ignition timing.
Temperature correction of idling speed ignition timing, principle
The value of "basic value idling speed ignition timing" is corrected with the current coolant and intake air temperature to obtain the correct effect to engine torque.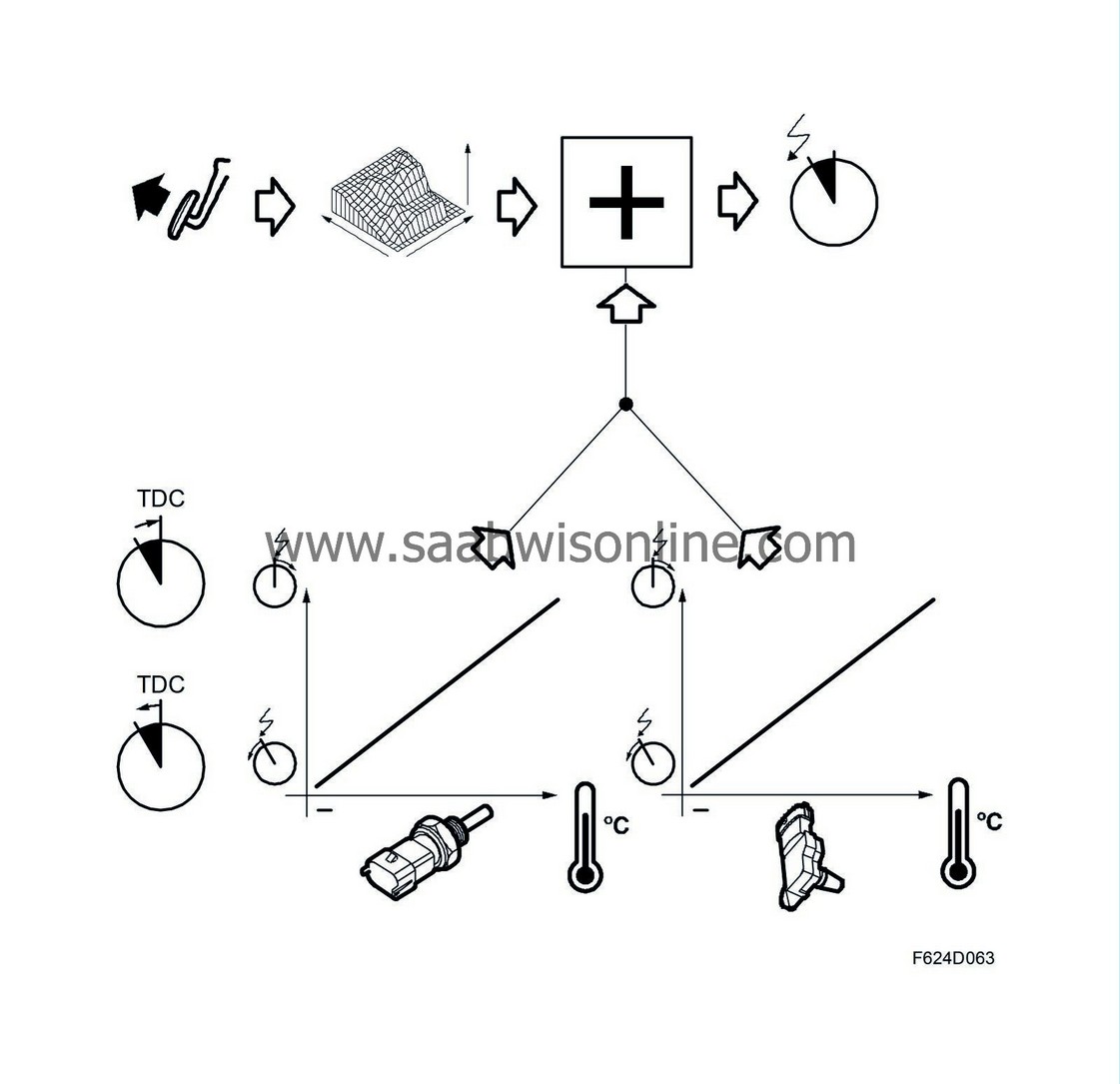
Correction, coolant temperature dependent
Low coolant temperature gives a positive compensation, i.e. the ignition timing is displaced to a somewhat more advanced value.
Correction, charge air temperature dependent
High intake air temperature gives a negative compensation, which means the ignition timing is displaced to a more retarded value.Ignition timing change for catalytic converter heating
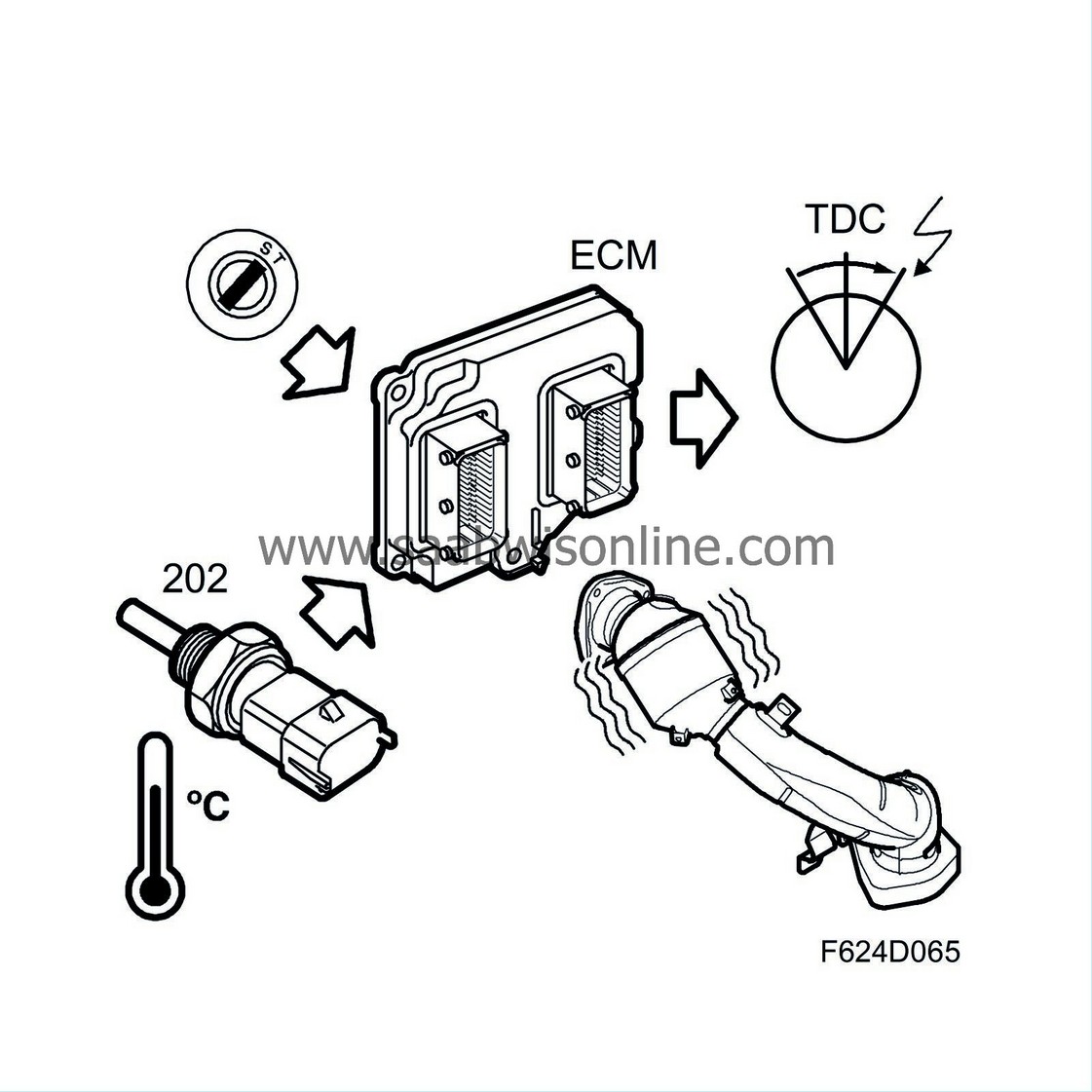
The "catalytic converter heating" function is activated during certain cold start conditions. This function causes a delay in ignition timing, usually after top dead centre together with the AIR function, which injects air into the exhaust ports.
As a result, exhaust gas temperature increases considerably and the catalytic converter is warmed up quickly.
This function is combined with slight opening of the throttle to compensate for the engine's reduced efficiency due to delayed ignition timing as well as to increase idling speed. This increases the air mass flow through the catalytic converters.
Anti-surge compensation

Surges (variations) may occur during acceleration. These are caused by sudden increases in engine torque combined with a certain elasticity in the power train and engine mountings. Through compensation, these vibrations can be reduced or eliminated completely.
The anti-surge function detects variations in engine speed and dampens them by influencing ignition timing, normally to a somewhat more retarded value.
Final ignition timing
Depending on whether ignition works in start, idling or normal mode, after all compensation the value will be converted to a signal that regulates the power amplifiers of the ignition coils for the six cylinders.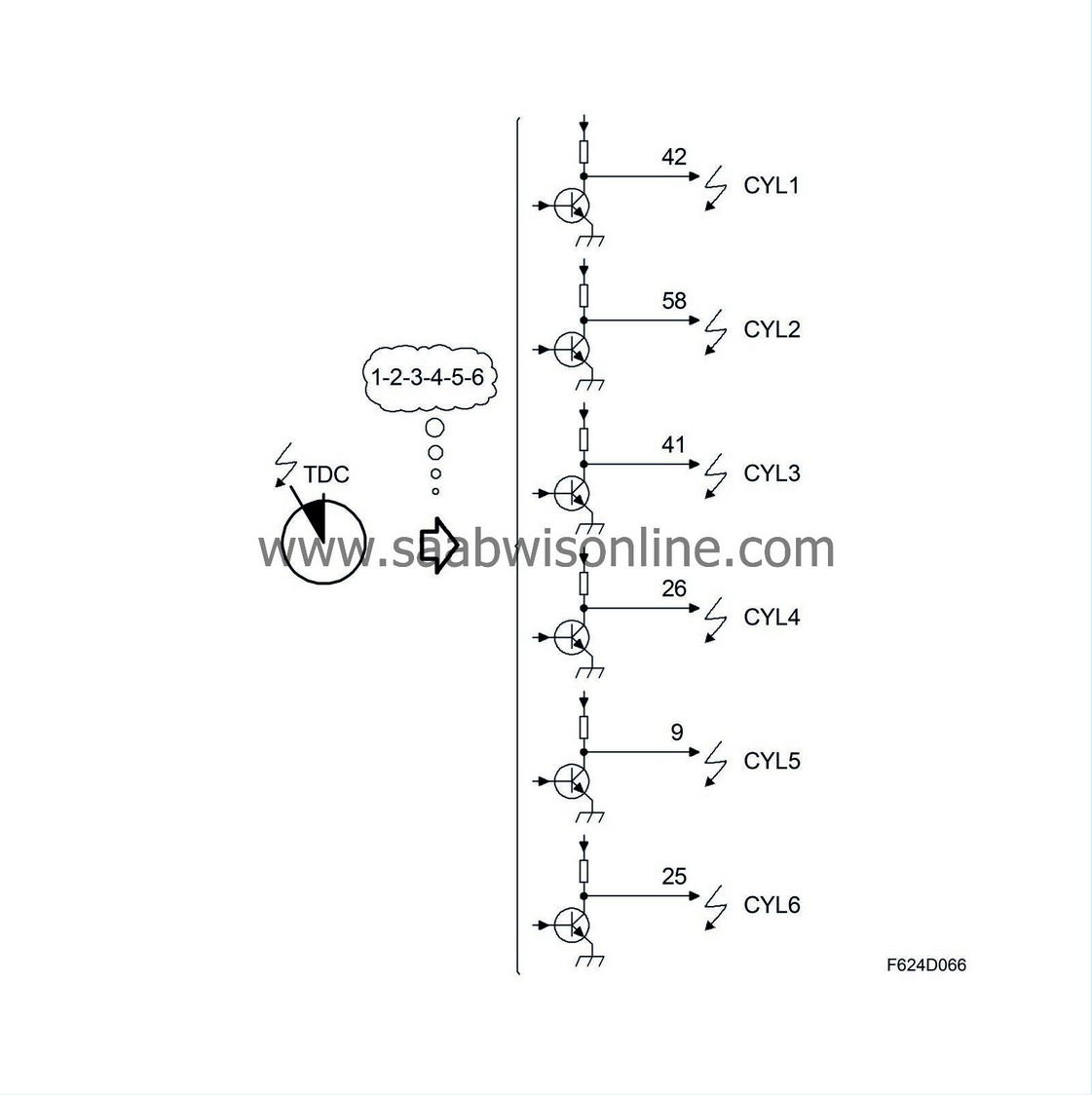